Otis ONE™ | Mechanic stories
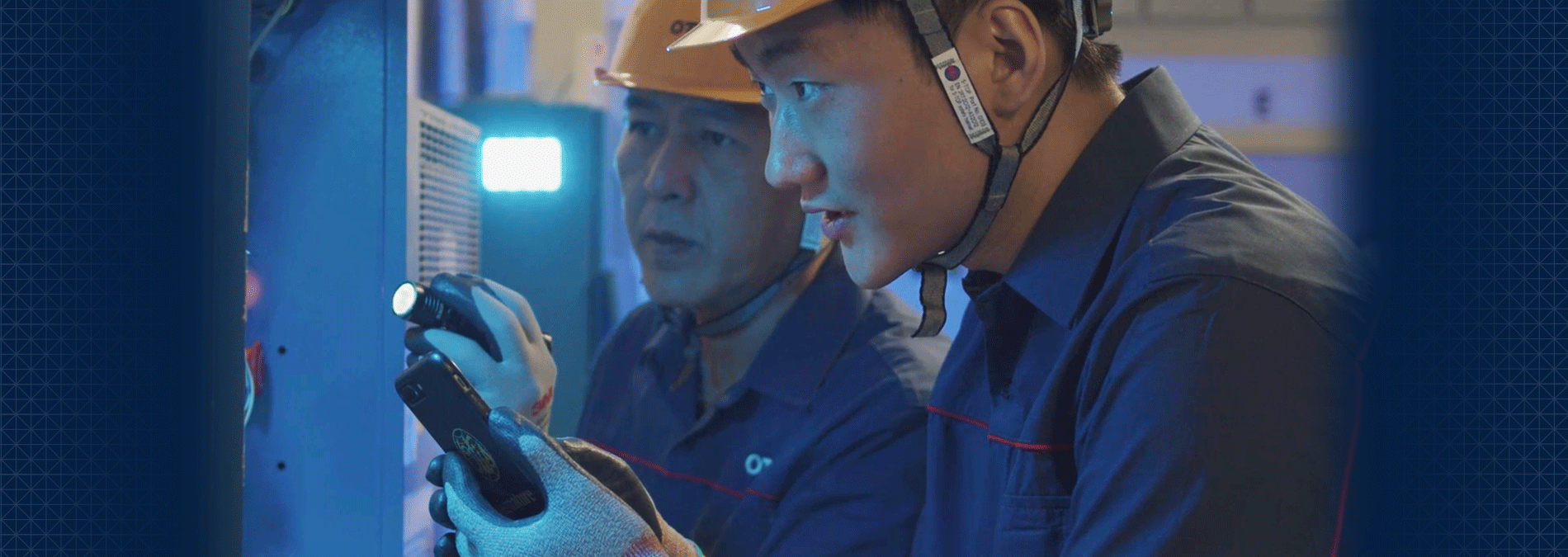
Our colleagues keep people moving
Hear what our mechanics are saying
Going Digital at Otis: How Otis ONE™ helps both mechanic and customer
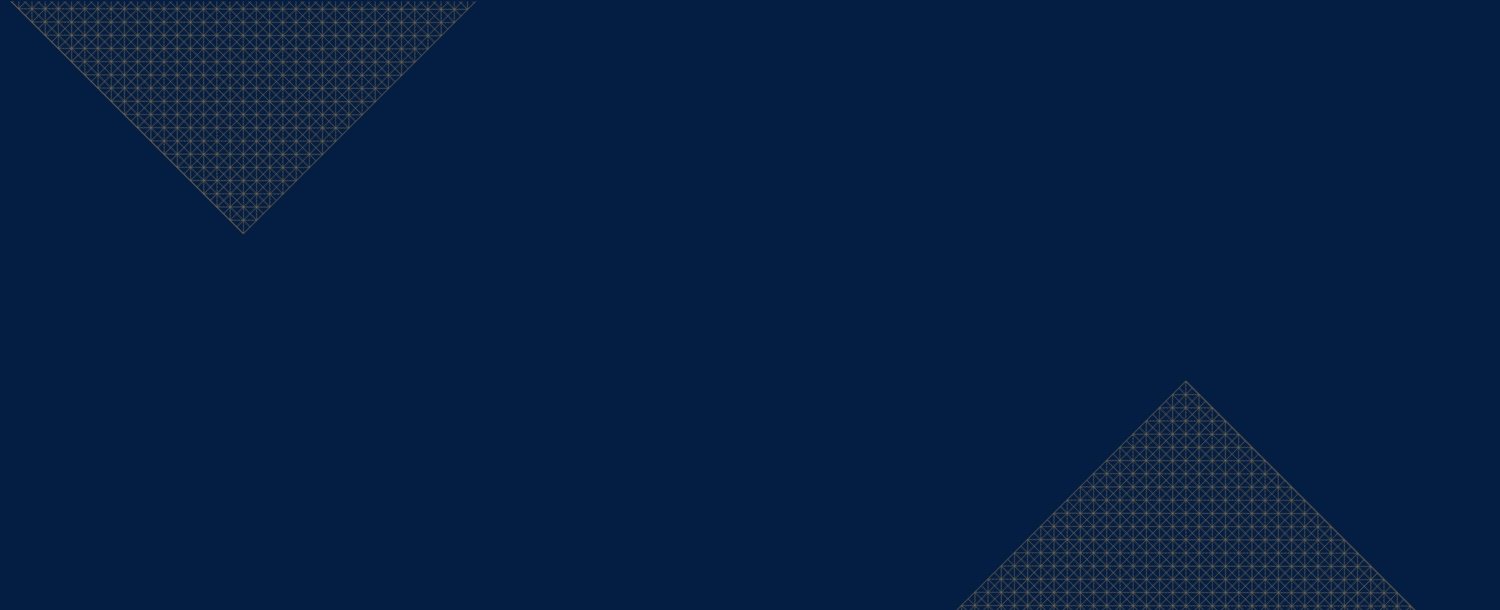
Information at your fingertips
Real-time data keeps Otis units running smoothly in Singapore
Otis ONE™ technology + our colleague’s skills and commitment = a win for customers
Otis Mechanic Gayas Q. enjoys troubleshooting and solving problems for his customers. With Otis ONE, he’s able to access information about elevator units -- right at his fingertips.
Using machine learning and cloud technology, Otis ONE provides our mechanics with predictive elevator maintenance insights, often allowing them to resolve issues before a customer reaches out. All Gayas needs to do is sign in to start troubleshooting any issues. When a callback comes, he can rely on Otis ONE™ to identify the event log.
This translates to greater efficiency and better deployment of resources for both parties – Otis and our customers. It is game changer,
he said. I am also able to obtain the replacement parts before going down to the jobsite. This saves me a lot of time and at the same time, I am able guide the junior mechanics I work with.
Gayas, who started his career as an electrical technician, has been with Otis Singapore for about 17 years. It makes me proud that I am playing a part to support Singapore’s urban infrastructure growth,
he said.
To perform well in the lift and escalator industry, you need to acquire specialized skillsets and technical knowledge,
he explained. Otis has provided me with the necessary training, and I now have the required technical knowledge to be working at Otis, the world’s leading company in this industry.
Real-time data keeps Otis units running smoothly in Singapore
Otis ONE™ technology + our colleague’s skills and commitment = a win for customers
Otis Mechanic Gayas Q. enjoys troubleshooting and solving problems for his customers. With Otis ONE, he’s able to access information about elevator units -- right at his fingertips.
Using machine learning and cloud technology, Otis ONE provides our mechanics with predictive elevator maintenance insights, often allowing them to resolve issues before a customer reaches out. All Gayas needs to do is sign in to start troubleshooting any issues. When a callback comes, he can rely on Otis ONE™ to identify the event log.
This translates to greater efficiency and better deployment of resources for both parties – Otis and our customers. It is game changer,
he said. I am also able to obtain the replacement parts before going down to the jobsite. This saves me a lot of time and at the same time, I am able guide the junior mechanics I work with.
Gayas, who started his career as an electrical technician, has been with Otis Singapore for about 17 years. It makes me proud that I am playing a part to support Singapore’s urban infrastructure growth,
he said.
To perform well in the lift and escalator industry, you need to acquire specialized skillsets and technical knowledge,
he explained. Otis has provided me with the necessary training, and I now have the required technical knowledge to be working at Otis, the world’s leading company in this industry.
Real-time data keeps Otis units running smoothly in Singapore
Otis ONE™ technology + our colleague’s skills and commitment = a win for customers
Otis Mechanic Gayas Q. enjoys troubleshooting and solving problems for his customers. With Otis ONE, he’s able to access information about elevator units -- right at his fingertips.
Using machine learning and cloud technology, Otis ONE provides our mechanics with predictive elevator maintenance insights, often allowing them to resolve issues before a customer reaches out. All Gayas needs to do is sign in to start troubleshooting any issues. When a callback comes, he can rely on Otis ONE™ to identify the event log.
This translates to greater efficiency and better deployment of resources for both parties – Otis and our customers. It is game changer,
he said. I am also able to obtain the replacement parts before going down to the jobsite. This saves me a lot of time and at the same time, I am able guide the junior mechanics I work with.
Gayas, who started his career as an electrical technician, has been with Otis Singapore for about 17 years. It makes me proud that I am playing a part to support Singapore’s urban infrastructure growth,
he said.
To perform well in the lift and escalator industry, you need to acquire specialized skillsets and technical knowledge,
he explained. Otis has provided me with the necessary training, and I now have the required technical knowledge to be working at Otis, the world’s leading company in this industry.
Real-time data keeps Otis units running smoothly in Singapore
Otis ONE™ technology + our colleague’s skills and commitment = a win for customers
Otis Mechanic Gayas Q. enjoys troubleshooting and solving problems for his customers. With Otis ONE, he’s able to access information about elevator units -- right at his fingertips.
Using machine learning and cloud technology, Otis ONE provides our mechanics with predictive elevator maintenance insights, often allowing them to resolve issues before a customer reaches out. All Gayas needs to do is sign in to start troubleshooting any issues. When a callback comes, he can rely on Otis ONE™ to identify the event log.
This translates to greater efficiency and better deployment of resources for both parties – Otis and our customers. It is game changer,
he said. I am also able to obtain the replacement parts before going down to the jobsite. This saves me a lot of time and at the same time, I am able guide the junior mechanics I work with.
Gayas, who started his career as an electrical technician, has been with Otis Singapore for about 17 years. It makes me proud that I am playing a part to support Singapore’s urban infrastructure growth,
he said.
To perform well in the lift and escalator industry, you need to acquire specialized skillsets and technical knowledge,
he explained. Otis has provided me with the necessary training, and I now have the required technical knowledge to be working at Otis, the world’s leading company in this industry.
Real-time data keeps Otis units running smoothly in Singapore
Otis ONE™ technology + our colleague’s skills and commitment = a win for customers
Otis Mechanic Gayas Q. enjoys troubleshooting and solving problems for his customers. With Otis ONE, he’s able to access information about elevator units -- right at his fingertips.
Using machine learning and cloud technology, Otis ONE provides our mechanics with predictive elevator maintenance insights, often allowing them to resolve issues before a customer reaches out. All Gayas needs to do is sign in to start troubleshooting any issues. When a callback comes, he can rely on Otis ONE™ to identify the event log.
This translates to greater efficiency and better deployment of resources for both parties – Otis and our customers. It is game changer,
he said. I am also able to obtain the replacement parts before going down to the jobsite. This saves me a lot of time and at the same time, I am able guide the junior mechanics I work with.
Gayas, who started his career as an electrical technician, has been with Otis Singapore for about 17 years. It makes me proud that I am playing a part to support Singapore’s urban infrastructure growth,
he said.
To perform well in the lift and escalator industry, you need to acquire specialized skillsets and technical knowledge,
he explained. Otis has provided me with the necessary training, and I now have the required technical knowledge to be working at Otis, the world’s leading company in this industry.
Real-time data keeps Otis units running smoothly in Singapore
Otis ONE™ technology + our colleague’s skills and commitment = a win for customers
Otis Mechanic Gayas Q. enjoys troubleshooting and solving problems for his customers. With Otis ONE, he’s able to access information about elevator units -- right at his fingertips.
Using machine learning and cloud technology, Otis ONE provides our mechanics with predictive elevator maintenance insights, often allowing them to resolve issues before a customer reaches out. All Gayas needs to do is sign in to start troubleshooting any issues. When a callback comes, he can rely on Otis ONE™ to identify the event log.
This translates to greater efficiency and better deployment of resources for both parties – Otis and our customers. It is game changer,
he said. I am also able to obtain the replacement parts before going down to the jobsite. This saves me a lot of time and at the same time, I am able guide the junior mechanics I work with.
Gayas, who started his career as an electrical technician, has been with Otis Singapore for about 17 years. It makes me proud that I am playing a part to support Singapore’s urban infrastructure growth,
he said.
To perform well in the lift and escalator industry, you need to acquire specialized skillsets and technical knowledge,
he explained. Otis has provided me with the necessary training, and I now have the required technical knowledge to be working at Otis, the world’s leading company in this industry.
Real-time data keeps Otis units running smoothly in Singapore
Otis ONE™ technology + our colleague’s skills and commitment = a win for customers
Otis Mechanic Gayas Q. enjoys troubleshooting and solving problems for his customers. With Otis ONE, he’s able to access information about elevator units -- right at his fingertips.
Using machine learning and cloud technology, Otis ONE provides our mechanics with predictive elevator maintenance insights, often allowing them to resolve issues before a customer reaches out. All Gayas needs to do is sign in to start troubleshooting any issues. When a callback comes, he can rely on Otis ONE™ to identify the event log.
This translates to greater efficiency and better deployment of resources for both parties – Otis and our customers. It is game changer,
he said. I am also able to obtain the replacement parts before going down to the jobsite. This saves me a lot of time and at the same time, I am able guide the junior mechanics I work with.
Gayas, who started his career as an electrical technician, has been with Otis Singapore for about 17 years. It makes me proud that I am playing a part to support Singapore’s urban infrastructure growth,
he said.
To perform well in the lift and escalator industry, you need to acquire specialized skillsets and technical knowledge,
he explained. Otis has provided me with the necessary training, and I now have the required technical knowledge to be working at Otis, the world’s leading company in this industry.
Real-time data keeps Otis units running smoothly in Singapore
Otis ONE™ technology + our colleague’s skills and commitment = a win for customers
Otis Mechanic Gayas Q. enjoys troubleshooting and solving problems for his customers. With Otis ONE, he’s able to access information about elevator units -- right at his fingertips.
Using machine learning and cloud technology, Otis ONE provides our mechanics with predictive elevator maintenance insights, often allowing them to resolve issues before a customer reaches out. All Gayas needs to do is sign in to start troubleshooting any issues. When a callback comes, he can rely on Otis ONE™ to identify the event log.
This translates to greater efficiency and better deployment of resources for both parties – Otis and our customers. It is game changer,
he said. I am also able to obtain the replacement parts before going down to the jobsite. This saves me a lot of time and at the same time, I am able guide the junior mechanics I work with.
Gayas, who started his career as an electrical technician, has been with Otis Singapore for about 17 years. It makes me proud that I am playing a part to support Singapore’s urban infrastructure growth,
he said.
To perform well in the lift and escalator industry, you need to acquire specialized skillsets and technical knowledge,
he explained. Otis has provided me with the necessary training, and I now have the required technical knowledge to be working at Otis, the world’s leading company in this industry.
Real-time data keeps Otis units running smoothly in Singapore
Otis ONE™ technology + our colleague’s skills and commitment = a win for customers
Otis Mechanic Gayas Q. enjoys troubleshooting and solving problems for his customers. With Otis ONE, he’s able to access information about elevator units -- right at his fingertips.
Using machine learning and cloud technology, Otis ONE provides our mechanics with predictive elevator maintenance insights, often allowing them to resolve issues before a customer reaches out. All Gayas needs to do is sign in to start troubleshooting any issues. When a callback comes, he can rely on Otis ONE™ to identify the event log.
This translates to greater efficiency and better deployment of resources for both parties – Otis and our customers. It is game changer,
he said. I am also able to obtain the replacement parts before going down to the jobsite. This saves me a lot of time and at the same time, I am able guide the junior mechanics I work with.
Gayas, who started his career as an electrical technician, has been with Otis Singapore for about 17 years. It makes me proud that I am playing a part to support Singapore’s urban infrastructure growth,
he said.
To perform well in the lift and escalator industry, you need to acquire specialized skillsets and technical knowledge,
he explained. Otis has provided me with the necessary training, and I now have the required technical knowledge to be working at Otis, the world’s leading company in this industry.
An Otis mechanic identified an elevator shutdown with Otis ONE™—before the customer even noticed
Located near one of the world’s busiest airports is a multi-story office complex boasting over 580,000 square feet of office and conference space. Thousands of office workers and conference guests rely on the building’s numerous elevators to get where they need to go each day. One early Monday morning last year, an elevator in the building was out of service in need of repair. To get it up and running, onsite technician support was needed. And on this particular day, the property was hosting a major conference, which made the situation even more critical. The shutdown had the potential to cause massive delays.
Luckily, Bernd J., an Otis mechanic with more than 30-years of experience, saw the problem on his Otis ONE app early that morning as soon as he started his day. The Otis ONE IoT digital platform uses artificial intelligence, machine learning and cloud technology to provide our mechanics with predictive maintenance insights and our customers with real-time information on the status of their elevators.
I usually check the app during breakfast to see if everything is ‘green’ — which means all units are running smoothly,
Bernd says. On this day, Bernd noticed one of the elevators at the customer site was shutdown requiring onsite support. Bernd hopped into his Otis van and was onsite by 7:30 a.m. The customer was surprised – and also very pleased – to see him there as the building staff had not yet noticed there was an elevator requiring repair.
Bernd’s dedication, supported by Otis ONE technology, allowed him to get the elevator back up and running before most of the office staff and conference guests had even arrived. The bottom line is Otis ONE means faster troubleshooting and higher system reliability for our customers,
added Bernd.
How Otis ONE™ keeps one university campus moving forward
Nestled in the heart of Atlanta, Georgia, an Otis customer brings together thousands of students and administrative staff members each semester to create the next generation of world leaders. With that mission in mind, keeping everyone moving on campus is essential.
The university relies on over 200 elevators, each one playing a key role in keeping students, faculty and administrators on the move. When an elevator is down, it disrupts operations and risks taking time away from the students' education.
Otis field professional Dwight P., responsible for elevator maintenance on campus, appreciates this. So he uses a different kind of learning — machine learning — with his Otis ONE™ app to save time on the job and keep his team working efficiently. The Otis ONE digital IoT platform uses artificial intelligence, machine learning and cloud technology to provide our customers with real-time information and our mechanics with predictive maintenance insights that help enhance elevator uptime.
On every call, I used to have to go to the machine room and sign into the controller to look at the fault log before I could even get started,
said Dwight. But with Otis ONE, it's all right in front of me on my smart phone, and it saves me valuable time on the job.
Otis ONE also helps Dwight prioritize which elevators need attention first, especially when multiple units across campus are reported to need service at once. Sometimes when an elevator is reported as not functioning, it's a false report, according to Dwight, so the Otis ONE solution helps the team on the ground assess the situation quickly.
Users sometimes report an elevator as not functioning by mistake or simply walking away while waiting, not realizing the elevator is running a diagnostic check,
said Dwight. With Otis ONE, I can see how recently an elevator door cycled — meaning how frequently it opened and closed — which allows me to see if a unit is actually out of service or not. This information helps me prioritize calls more effectively and keeps my team from ping-ponging all over campus, saving lots of time.
Learn more about Otis ONE and how it can save your site time and money.