Sample Templates 2
Structure Name:-Text Strip with Image at Center Structure
Template Name:-Text Strip with Image at Center Template
Image Size:-Width:500px and Height:400px
Read all about it
Our relentless commitment to safety, ethics and quality in every choice we make leads to our business success.
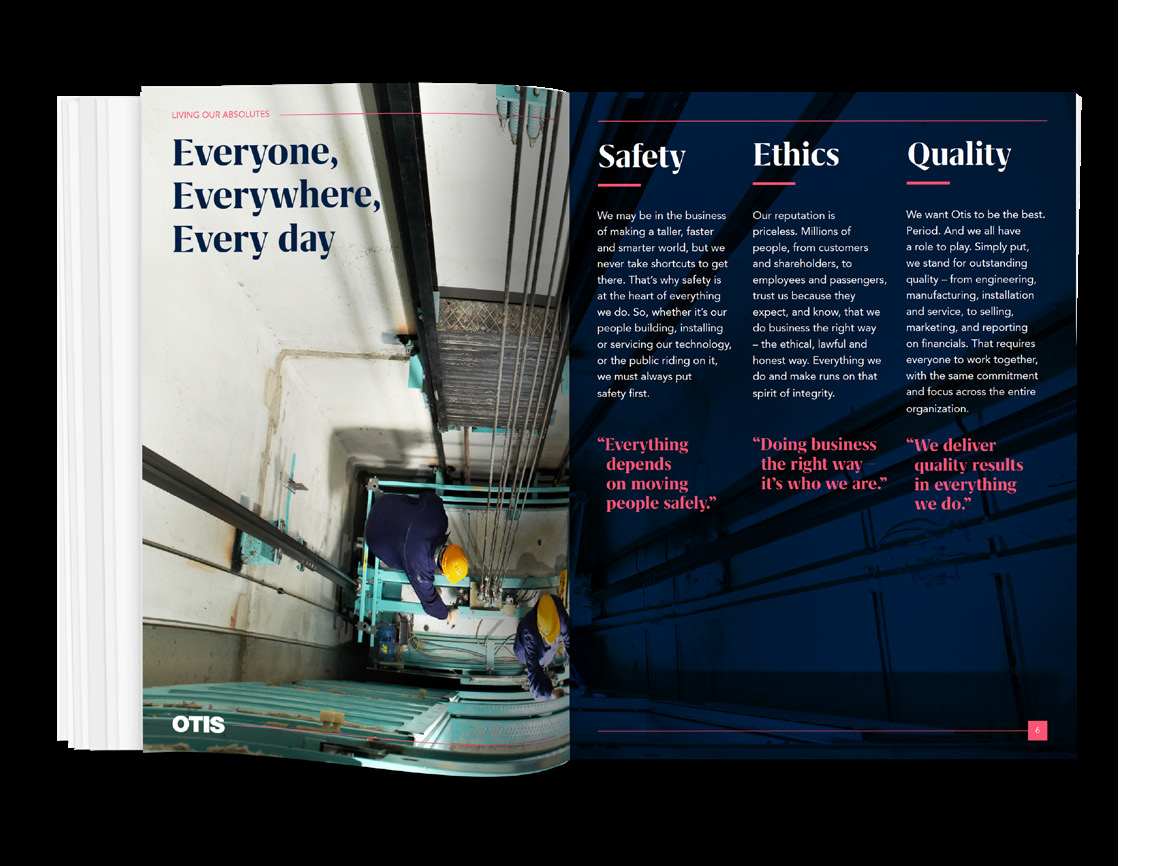
Structure Name:-Generic Textstrip and Image on the RightSide Structure
Template Name:-Generic Textstrip and Image on the RightSide Template
Image Size:-Width:600px and Height:600px
Going above and beyond
When it comes to safety, just meeting code is not enough. The sheer breadth of our additional features stand testament to our dedication to your safety. Employing the very best materials and precision engineering methods, we provide failsafe freedom of choice.
-
1 Acrylic wedge guard deflectors
-
2 Increased height anti-fall balustrade
-
3 Painted yellow demarcation lines
-
4 Aluminum steps
-
5 Rounded step nose (4 mm radius)
-
6 Anti-climb barrier panels
-
7 Black or aluminium profile brush guards
-
8 Yellow-coated combs
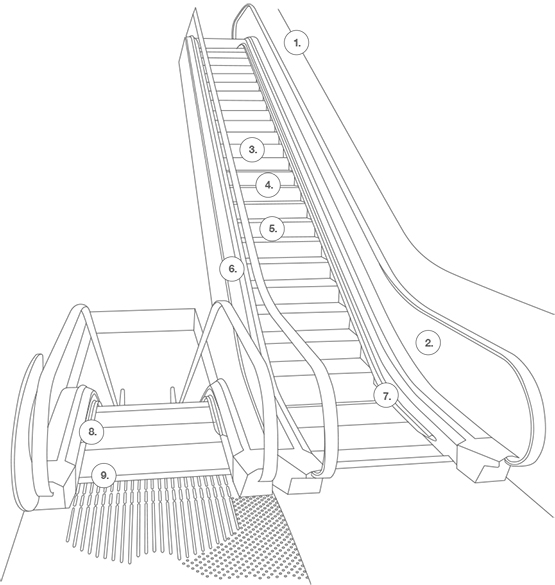
Structure Name:-Featured Icon Card Structure
Template Name:-Featured Icon Card Template
Image Size:-Width:80px and Height:80px
Structure Name:-Text Strip with Images Structure
Template Name:-Text Strip with Image Heading Template
Image Size:-Width:1200px and Height:350px

More than 1 million sold with installations in nearly 200 countries

Reduced energy consumption by 75%

Leading the digital evolution of elevators for 20 years
Structure Name:-Hubspot Form Structure
Template Name:-Hubspot Form Template
No Image in this Module
Advanced 24/7 monitoring of critical elevator systems in cab, machine room, hoistway, and pit
Cloud-based data analytics
Informed mechanic resolves issues more quickly
Building manager tracks elevator performance and service delivery in Otis Customer Portal
Structure Name:-File View Structure
Template Name:-File View 1 Tab Template
No Image in this Module
Structure Name:-List Structure
Template Name:-List 3 Tabs Template
No Image in this Module
- Women on the Rise: Otis Colleagues Recognized by Paradigm for Parity®
- Otis Recognized by Seramount as Leading Inclusion Company
- Disability Equality Index® Best Place to Work for Disability Inclusion’ in Five Countries 2024
- TOP 100 GLOBAL INNOVATORS – CLARIVATE, 2025
- Top 100 Global Innovators - Clarivate, 2024
- Top 100 Global Innovators - Clarivate, 2023
- World’s Best Employers List – Forbes, 2024
- World's Best Employers List - Forbes, 2023
- World's Best Employers List - Forbes, 2022
- World's Top Companies for Women - Forbes, 2023
- World’s Top Female-Friendly Company - Forbes, 2022
- Best Place to Work for LGBTQ+ Equality - Human Rights Campaign Foundation, 2022
- Best Place to Work for LGBTQ+ Equality - Human Rights Campaign Foundation, 2021
- Distinguished Leadership Award: Chair & CEO, Judy Marks - The Conference Board's Committee for Economic Development, 2021
- Excellence in Corporate Social Responsibility - Communitas Award, 2022
- Excellence in Corporate Social Responsibility - Communitas Award, 2021
- Most Admired Company - Fortune, 2025
- Most Admired Company - Fortune, 2023
- Most Admired Company - Fortune, 2022
- Noteworthy Company - Fair360 (formerly DiversityInc), 2024
- Noteworthy Company - DiversityInc, 2023
- Noteworthy Company - DiversityInc, 2022
- GLobal inclusion index company - Seramount, 2023
- Project of the Year: Elizabeth line in London - Elevator World, 2024
- Project of the Year: Singapore MRT - Elevator World, 2024
- Project of the Year: 22 Bishopsgate in London - Elevator World, 2023
- Project of the Year: East Rail Line Cross-Harbour Extension in Hong Kong - Elevator World, 2023
- Project of Year: Taichung MRT in Taipei, Taiwan - Elevator World, 2022
- Project of the Year: Collins House in Melbourne, Australia - Elevator World, 2021
- Project of the Year: Yitzchak Navon Train Station in Jerusalem - Elevator World, 2021
- Project of the Year: Modernization, Empire State Building in New York - Elevator World, 2020
Structure Name:-Textstrip with Background Color Structure
Template Name:-Textstrip with Background Color Template
No Image in this Module
Structure Name:-Info Cards Structure
Template Name:-Info Cards Horizontal Template
Image Size:-Width:350px and Height:300px
Explore ways we are helping you stay safer while on the move
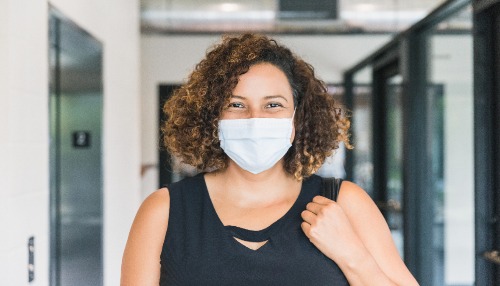
Ride with confidence
Wondering about the risks of riding in an elevator right now? Explore study findings about the airflow within elevators and read objective answers, backed by research and data, from leading air quality expert .
Explore the Study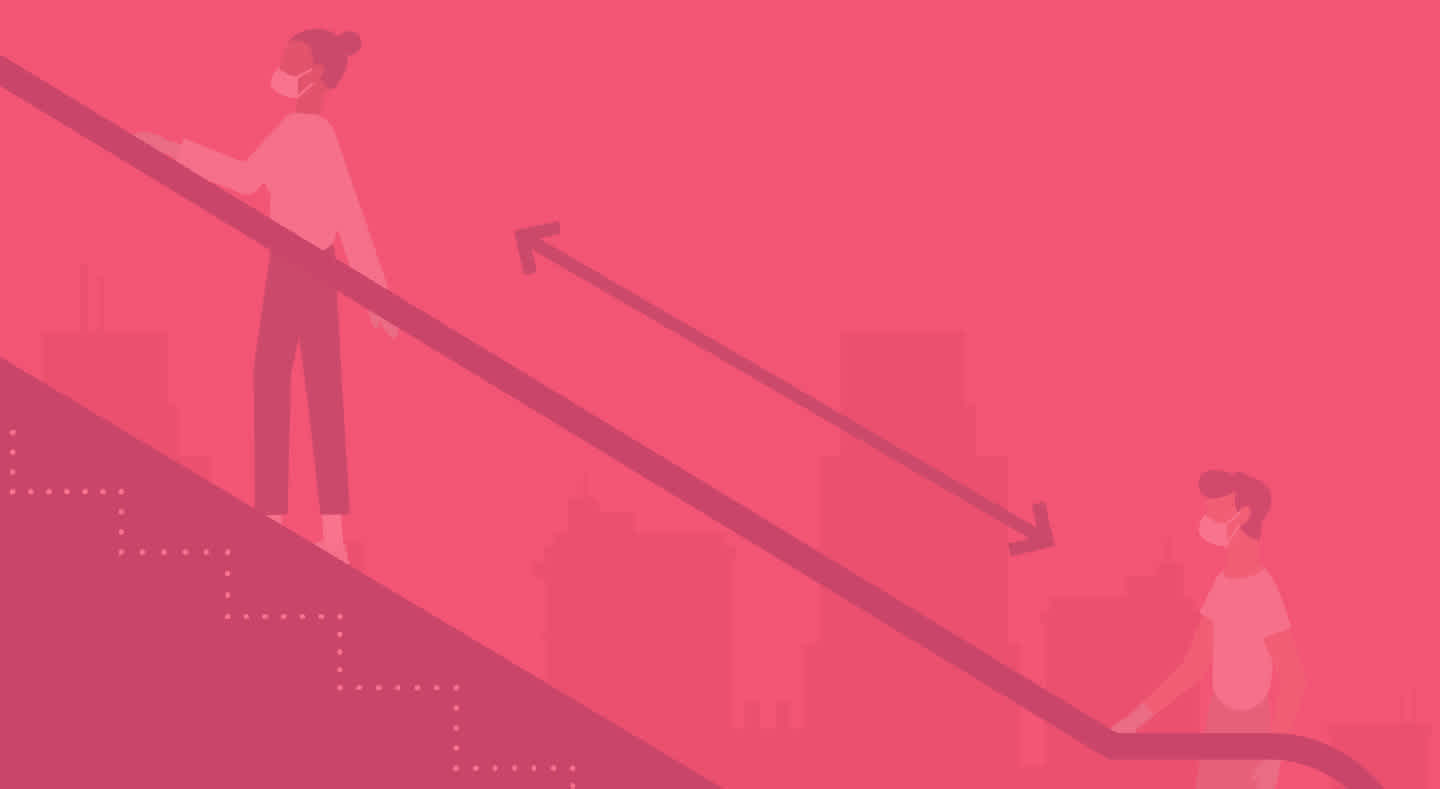
Rethinking The Way You Ride
Social distancing. Hand sanitization. Proper equipment cleaning. Both riders and building owners can take simple steps to reduce exposure and enhance safety. Browse our resources to learn more.
BUILDING MANAGER TIPS(PDF)Why choose Otis Service
Today, we’re doubling down on his promise of personalised service and how we deliver it through our local service teams across the UK.
We’re harnessing emerging technologies and the Internet of Things to deliver the personalised experience people know and want in today’s digital age. Our teams are smarter, our customers are more informed and our equipment is more efficient. At the same time, passengers enjoy the safety and comfort we’ve been known for all these years. It’s modern intelligence to support a legacy of personal touch.
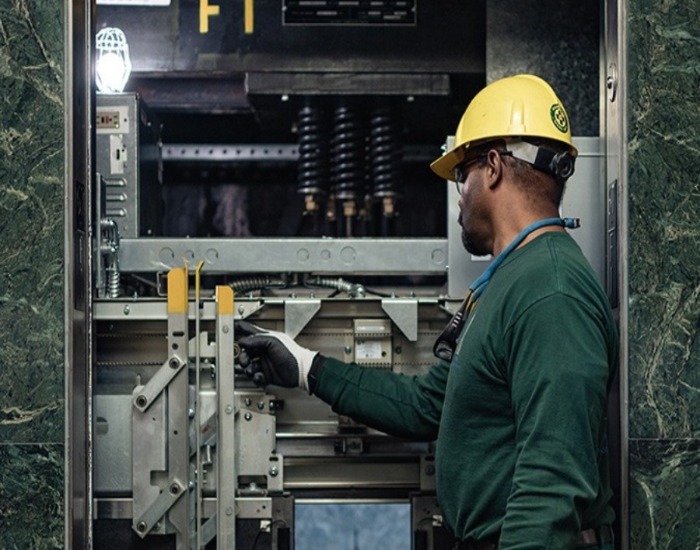
Engineering expertise
Engineers are the lifeblood of our organization and the face of Otis. To provide the best possible service, we have over 400 engineers, trained to a minimum of NVQ Level 3, and located right across the UK. Furthermore, through our apprentice scheme, we train and develop a constant stream of engineers who not only gain academic and Otis specific product knowledge, but also invaluable experience via the fully qualified engineers whom they work closely with.
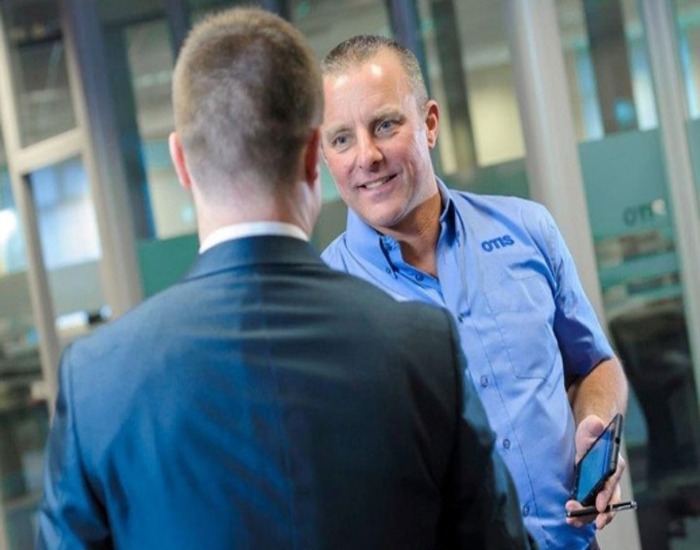
Safety is our No.1 Priority
Safety is a core value at Otis and therefore influences everything we do. Our safety standards surpass industry guidelines, which is why our incident levels are consistently lower than the industry average. In addition, all our engineers undertake regular training and are consistently audited by third party organisations to help ensure everyone’s safety.
Managing your insurance reports
It is a legal requirement for you to arrange an inspection of your equipment every 6 months by a third party. Once this inspection has been completed, we make it easy for you to manage any work requirements, which ultimately helps to keep your equipment safe for passengers. Just send the report to our dedicated team at ukinsrepts@otis.com. The report will generate a work order which will be sent directly to your engineer’s PDA.
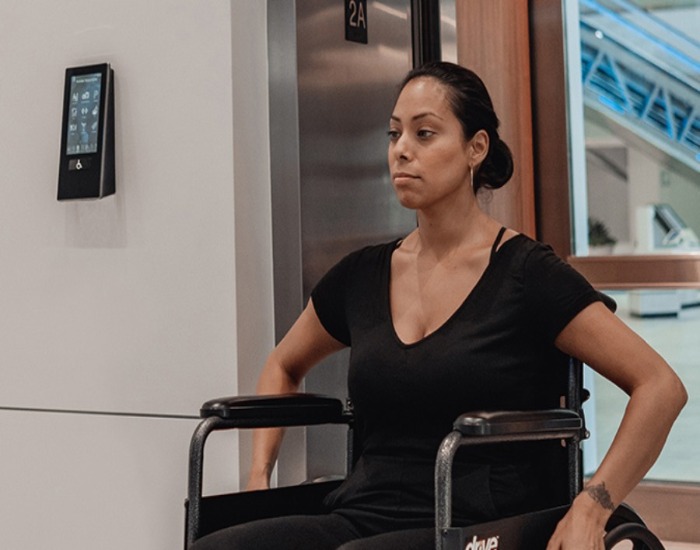
Spare parts same day UK service
With a vast 80,000 components catalogued and 25,000 parts in stock, the Otis European Parts Centre can dispatch within 24 hours.
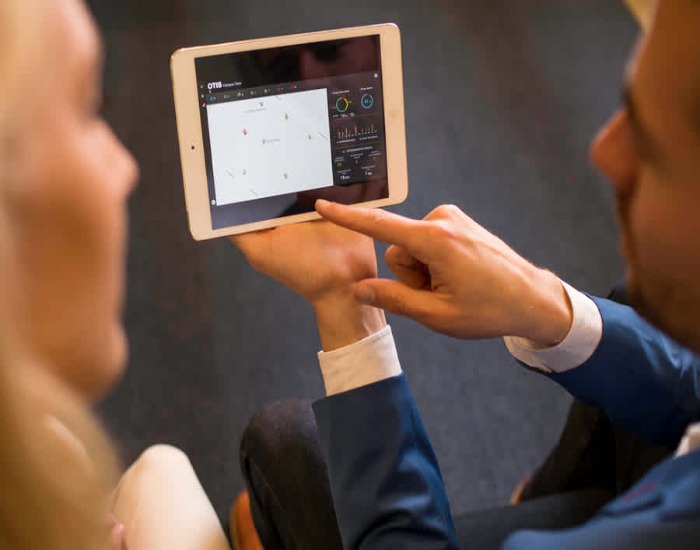
24/7 Support
Whether you have questions about contracts, invoicing, maintenance, equipment or passenger support, you can call or click to chat with a service representative at any time.
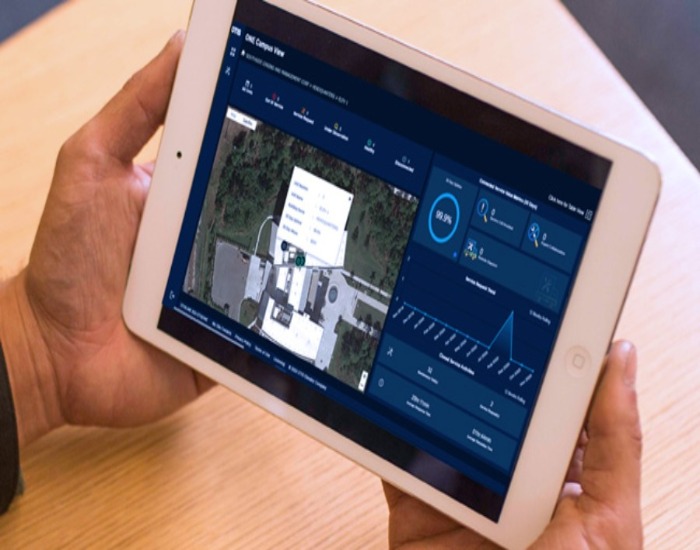
Customer portal
The Otis customer portal is accessible anytime from your computer, tablet or mobile device. Use it to manage your entire lift, escalator and moving walkway portfolio. It has been designed to enable you to: Stay up-to-date with your lift service history and performance data. See how many service calls a particular unit has had and when your maintenance visits took place, plus the levels of uptime for each unit. The portal will also provide you details of your Sales, and Service Delivery Managers at Otis so you can get in touch.
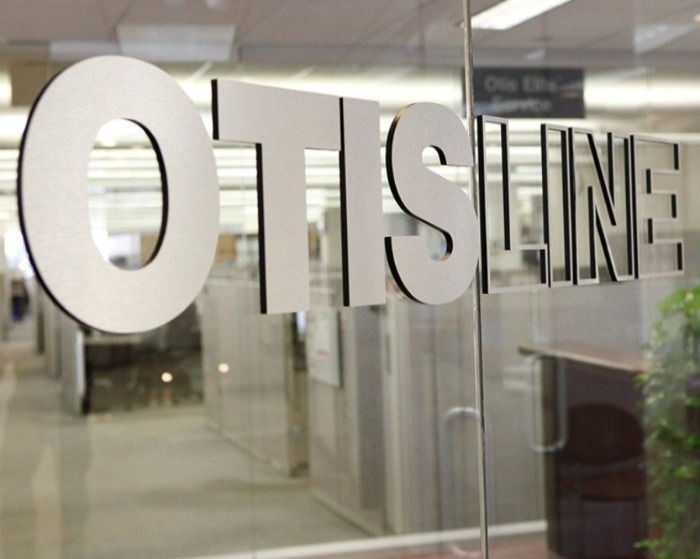
Otisline
Available 24 hours a day, 365 days per year, Otisline® is our dedicated in-house customer care facility. The team can be reached on 0800 181363.
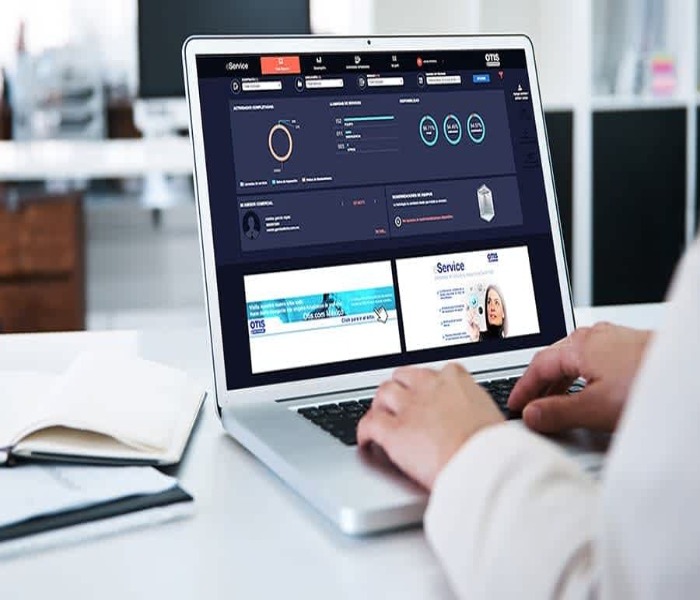
Our apps to improve our service delivery
We have developed a range of digital tools to provide an unsurpassed service for our customers. With this advanced technology, our engineers can monitor, diagnose issues and potentially fix your equipment remotely. Ultimately our technology will help predict issues, resulting in fewer service calls and accelerated response time.