High-Rise Safety Systems
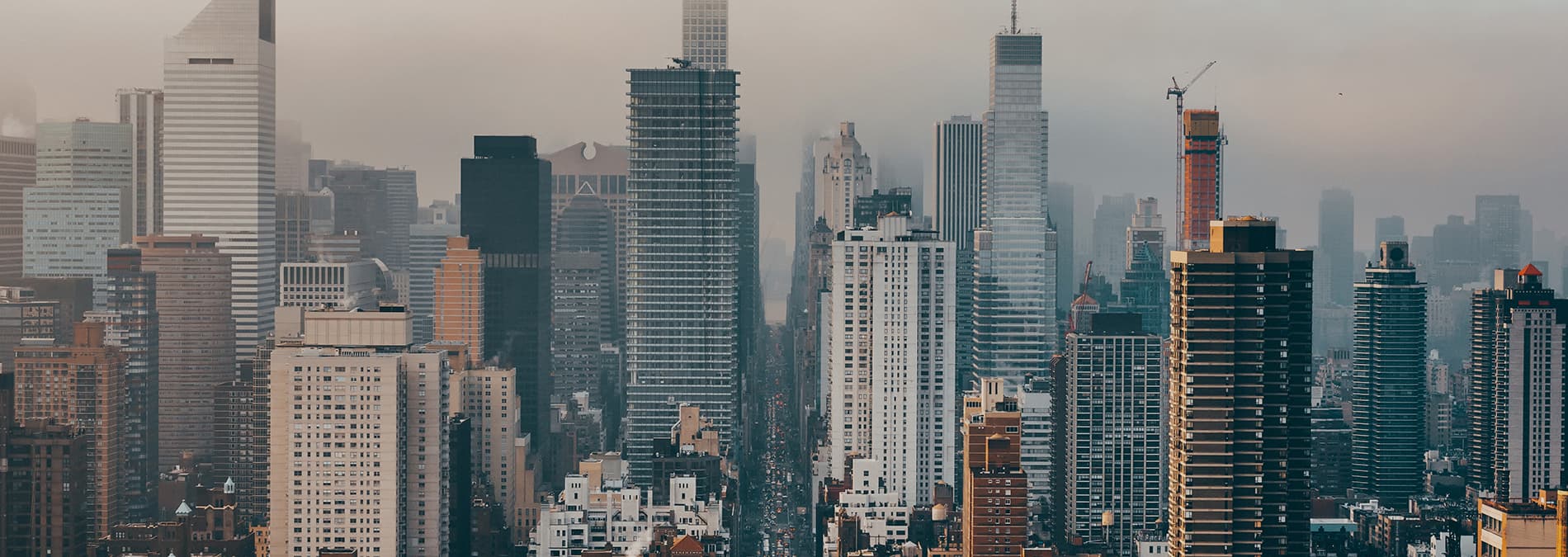
High-Rise Safety Systems
Safety systems in a modern high-rise elevator
The Greek mathematician Archimedes is generally credited with creating the first elevator-like device in the third century B.C. But elevators only became a safe, reliable means of transportation for people after 1852 – the year Elisha Otis invented the elevator safety brake.
An inspired piece of engineering, Otis’ safety brake kept the elevator from falling if the hoisting rope broke. If the rope went slack, the release of tension triggered the safety brake – a large leaf spring that snapped into notches cut into rails that supported the elevator on opposite sides of the elevator car.
The safety systems in modern high-rise elevators are infinitely more advanced than Elisha Otis’ original device, incorporating sophisticated technologies developed over generations by engineers working in areas like advanced computing, sensor technology and materials science.
Here’s a look at how these precision-engineered systems work – and why you should feel safe riding in a properly maintained elevator in one of today’s supertall buildings.
Engineered for safety
Modern elevators have two basic sets of safety components: electrical and mechanical.
The electrical components include the elevator controller, sensors and software systems. The elevator’s controller serves as the brains of the system. Sensors monitor safety-related functions like car speed and position, and door-lock state or access panel position; and they send the data back to the controller. Software systems provide independent assessment to validate redundant sensor systems.
The mechanical components include the elevator machine itself, the machine brake, the overspeed governor, the safety brakes (also known as the car safeties) and, finally, the buffers at the bottom of the hoistway.
The suspension cables themselves are also essential components of the safety system. High-rise elevators today move up and down on many cables – far more than are needed to support a fully loaded car.
Key safety features
-
1 The controller
Microprocessor-based controllers are the brains of the system, controlling all elevator functions based on data received from multiple subsystems, components and sensors.
-
2 The machine
The gearless machine consists of a motor, traction sheave and brake. The sheave drives the cables attached to the elevator car and counterweight. In a gearless traction machine, the drive sheave is an integral part of the motor.
-
3 The brakes
Modern elevators use friction brakes: a pair of shoes that apply equal and opposite pressure to a drum, pulley or disc mounted on the motor shaft. Springs apply the brake shoes to the pulley and are lifted electrically. If power is lost, the brake applies.
-
4 The governors
The governor continuously monitors car speed. If the car exceeds its maximum rated speed, flyweights inside the governor spring outward, causing the governor to initiate action: first engaging the machine brake, then engaging the car
-
5 The safeties
Located on the elevator car itself, the safeties grab the hoistway rails when activated.
-
6 The buffer
Positioned at the bottom of the hoistway, buffers can absorb and dissipate the energy of a descending elevator.
Download PDF
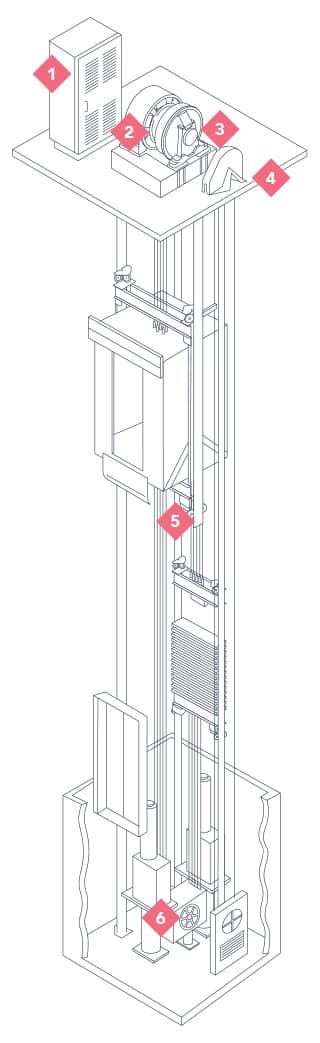
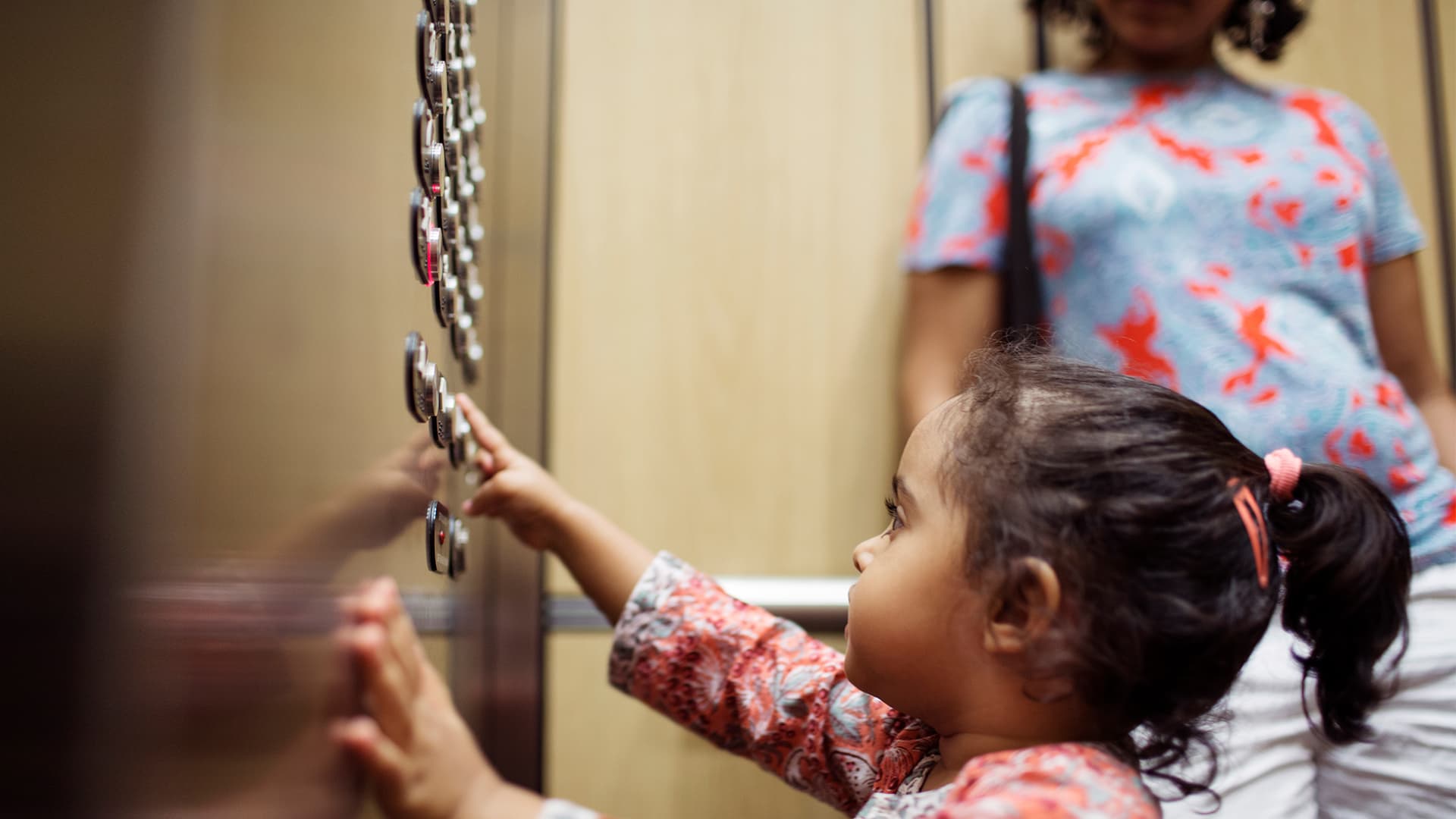
Sample scenario
In describing the safety system in today’s high-rise elevators, engineers talk about a safety chain.
It’s a metaphor that turns the familiar proverb on its head. One break in the chain and the elevator stops until the issue is resolved. This constitutes its strength.
Suppose an elevator exceeds its rated speed by a certain percentage: a link in the safety chain has been opened, triggering the control system to safely stop the elevator.
In this case, the elevator’s sensors communicate the increase in speed to the controller, which initially modifies current to the machine to slow down the elevator. At this point, the machine brake hasn’t been applied. The machine itself is slowing down the elevator. The process is similar to downshifting in an automobile with a manual transmission instead of stepping on the brake.
If modifying current to the machine doesn’t slow the elevator enough, the controller then removes all power from the machine and applies the machine brake, slowing the elevator further. The safety system is designed (per applicable codes) to bring the elevator to a controlled stop.
If the elevator continues to accelerate – or overspeed
in engineering jargon –the governor is the next component in the safety hierarchy to be activated.
The governor is a speed-sensing device mounted in the machine room. It has its own pulley, moved by a steel cable (the governor rope) that is attached to the elevator car – meaning it moves at the same speed as the elevator. If the governor spins too fast, flyweights inside the governor spring outward, tripping a device that grabs the governor rope.
The now-motionless governor rope pulls on the safeties – essentially emergency brakes on the car itself – and engages them. The safeties clamp onto the hoistway rails, bringing the elevator to a safe stop.
These safeties are the modern version of Elisha Otis’ original safety brake.
Buffers come into play if the other braking components don’t have enough time to bring the elevator to a complete stop by the time the elevator reaches the bottom of the hoistway. They slow the car to a stop, acting like giant automotive shock absorbers.
Advances in safety
As reliable as these safety-systems are, research engineers are constantly developing new technologies that continue to improve performance.
A relatively recent innovation is known as PESSRAL: Programmable electronic system in safety-related applications for lifts. With advances in programmable electronic systems, the control systems have gotten even smarter. Instead of knowing only that a link in the safety chain is open, they can identify which link is open – and tailor the response based on the situation.
The control system’s response becomes more like how people respond behind the wheel of an automobile: sometimes they choose to change lanes; other times, they decide to come to a complete stop. With PESSRAL, the controller becomes smarter and acts with a customized response to an issue instead of having only one choice available: stopping the elevator and preventing its operation.
Summary
Since Elisha Otis’ invention of the safety brake, the safety features on elevators have evolved into fully integrated systems comprising mechanical components, smart controllers and advanced electronics – with multiple safety redundancies built in. With all of these measures in place, elevators provide a safe, reliable and convenient mode of transportation.
More than that, elevators have played an indispensable role in creating the connected urban world of today. According to the United Nations, 55 percent of the world’s population lives in cities today, or about 4.2 billion people, a figure that is expected to reach nearly 70 percent by the year 2050.
It is impossible to imagine this world without elevators.