Cruise ships | Otis Global Projects
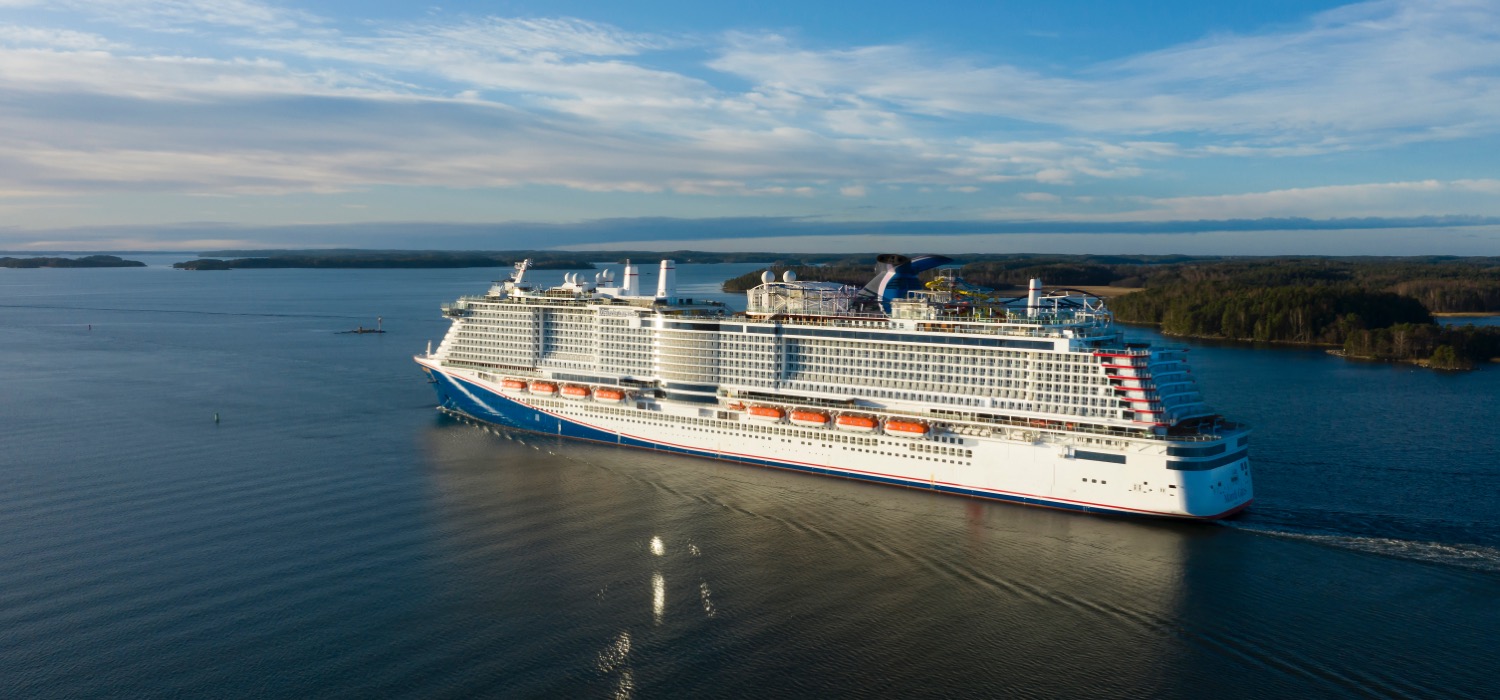
Cruise Ships
Europe
How specialized products for the maritime environment led one of the world’s leading ship builders to turn to Otis
Next-generation cruise liners require durability, reliability and an elevated passenger experience. With expertise in this specialized market, Otis works alongside world-renowned ship builder Meyer Group to ensure these vessels were ready to meet crew and passenger expectations.
Vessel Facts
Unique Requirements
The always moving maritime environment is a challenge for the durability of materials at sea. This requires a specialized elevator design. To provide safe and efficient service for crew and guests, maritime elevators have specialized software configuration. In heavy rolling seas, the elevators on ships are programed to detect excessive motions and park automatically on pre-determined decks to avoid damage.
Servicing elevators and escalators on board cannot be managed like in buildings. To ensure elevators and escalators run smoothly and safely, the crew onboard are specifically trained by Otis and provided extensive remote support to perform routine checks and tackle issues.
Otis Innovation
For the first four vessels delivered by Meyer Shipyards, Otis transported and installed special operating features such as luggage mode, gangway deck mode and RFID-based priority service, ReGen drives for energy efficiency and also installed:
88 passenger elevators
24 maritime escalators
8 freight lifts
Remote support to perform routine checks and tackle issues
68 service elevators
6 handicapped lifts
EMS PanoramaTM Elevator Management System
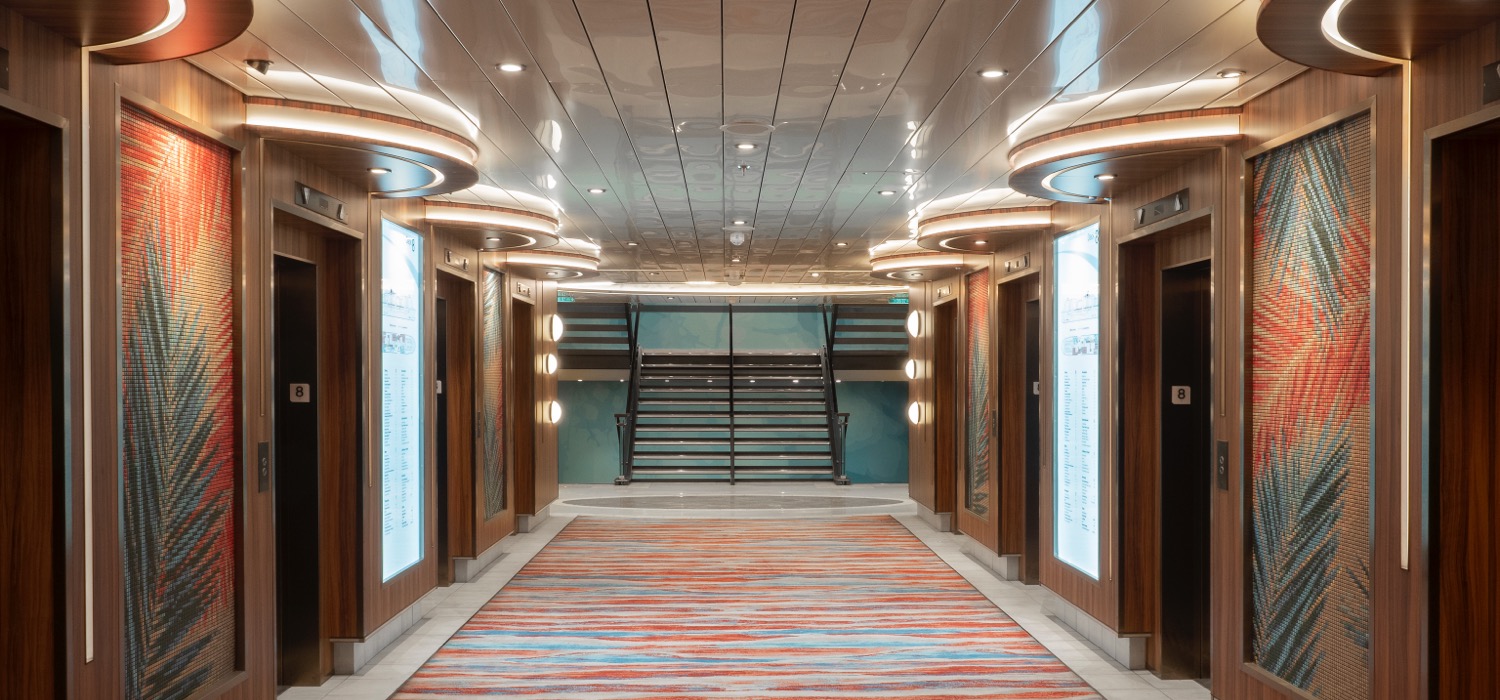
Otis delivered and installed more than 190 specialized elevators and escalators for four cruise ships
Performance and style
Elegance, refinement and style are words often associated with cruises.
Every detail on a ship contributes to that impression. Otis builds in aesthetics during project development and the elevators are customizable from car interiors to landing doors, so they match the ship’s unique theme and design.
Elevators and escalators on cruise ships are subject to heavy traffic. On average, passenger lifts record 2,000 runs per day.
This figure reflects the important role elevators and escalators play in the comfort and experience of passengers and in the quality of service provided by the crew.
This is particularly noticeable during peak demand periods; for instance, when a large number of passengers board or get off the ship for trips on land.
Otis Marine: Experts in the maritime segment
With more than 100 years of experience in the marine industry, Otis Marine provides a single point of contact for customers in this unique segment.
Most units are manufactured at Otis’ specialized factory in Vigo, Spain. Otis Marine products serve all marine segments, including cruise ships, ferries, commercial ships, offshore platforms and naval vessels.
Installation crews work in the shipyard as the vessel is being assembled. Otis Marine provides 24/7/365 service worldwide. Its products are certified by major Class Societies and complies with ISO8383.
Solution
The always moving maritime environment is a challenge for the durability of materials at sea. This requires a specialized elevator design. One example of this is in the maneuver cable, one of the elevator’s core mechanical parts. In maritime elevators it has been exclusively redesigned to sit in an anti-oscillating chamber to protect it from scratches and breakages when the ship tilts.
To provide safe and efficient service for crew and guests, maritime elevators have specialized software configuration. In heavy rolling seas, the elevators on ships are programed to detect excessive motions and park automatically on pre-determined decks to avoid damage. When passengers are in the car during rolling or pitching, thanks to this special mode, the elevator takes them to the exit deck (gangway) defined by vessel managers from a single push of a button.
These cruise vessels travel the world throughout the year. Servicing elevators and escalators on board cannot be managed like in buildings. To ensure elevators and escalators run smoothly and safely, the crew onboard are specifically trained by Otis and provided extensive remote support to perform routine checks and tackle issues. More advanced maintenance operations and technical assistance are performed by a team of Otis Marine experts who travel the world to meet the ships.
Featured Solutions
Relevant Projects
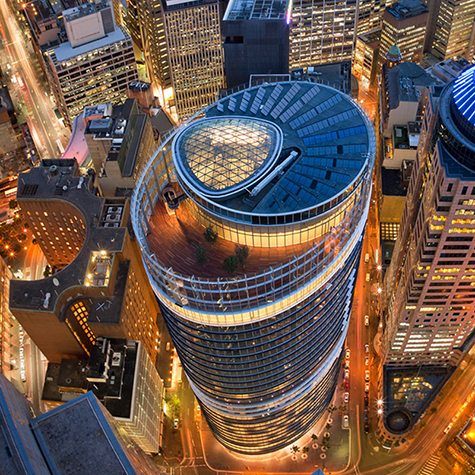
1 Bligh Street
Sydney, Australia
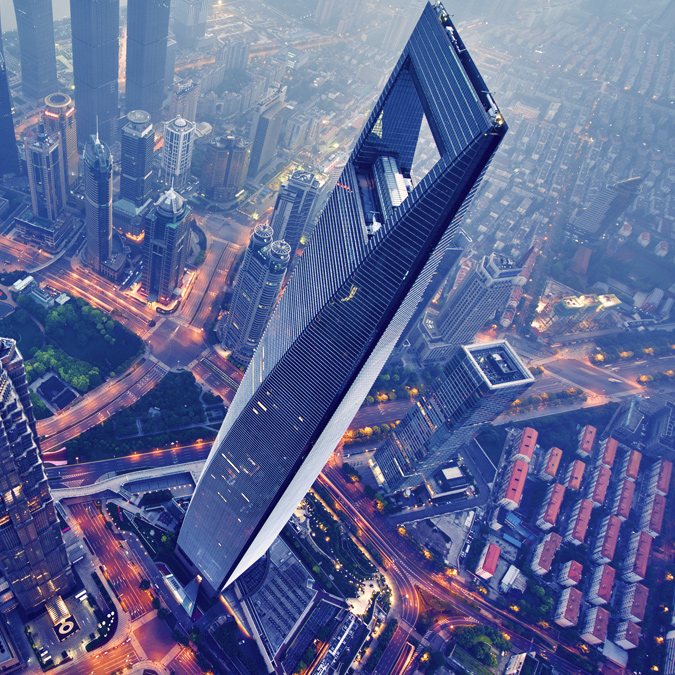
Shanghai World Financial Center
Shanghai, China
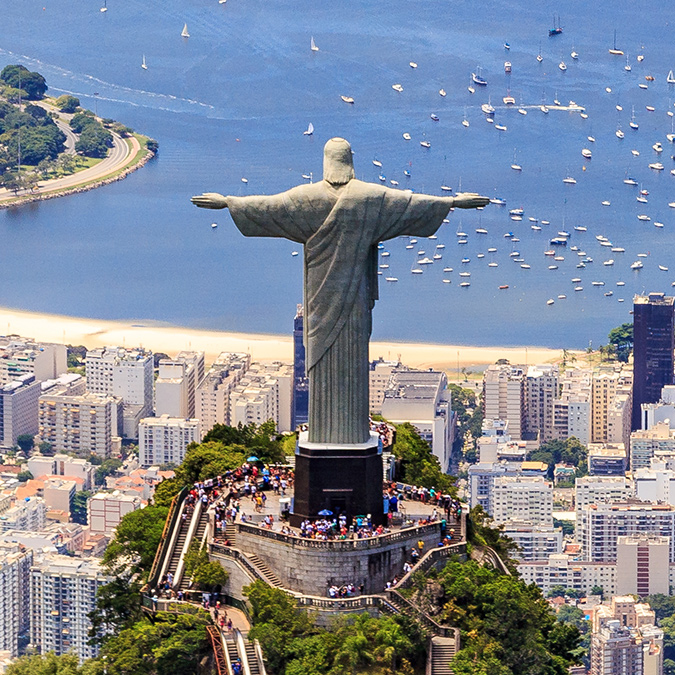
Christ The Redeemer
Rio de Janeiro, Brazil