Otis ONE™ | Mechanic stories
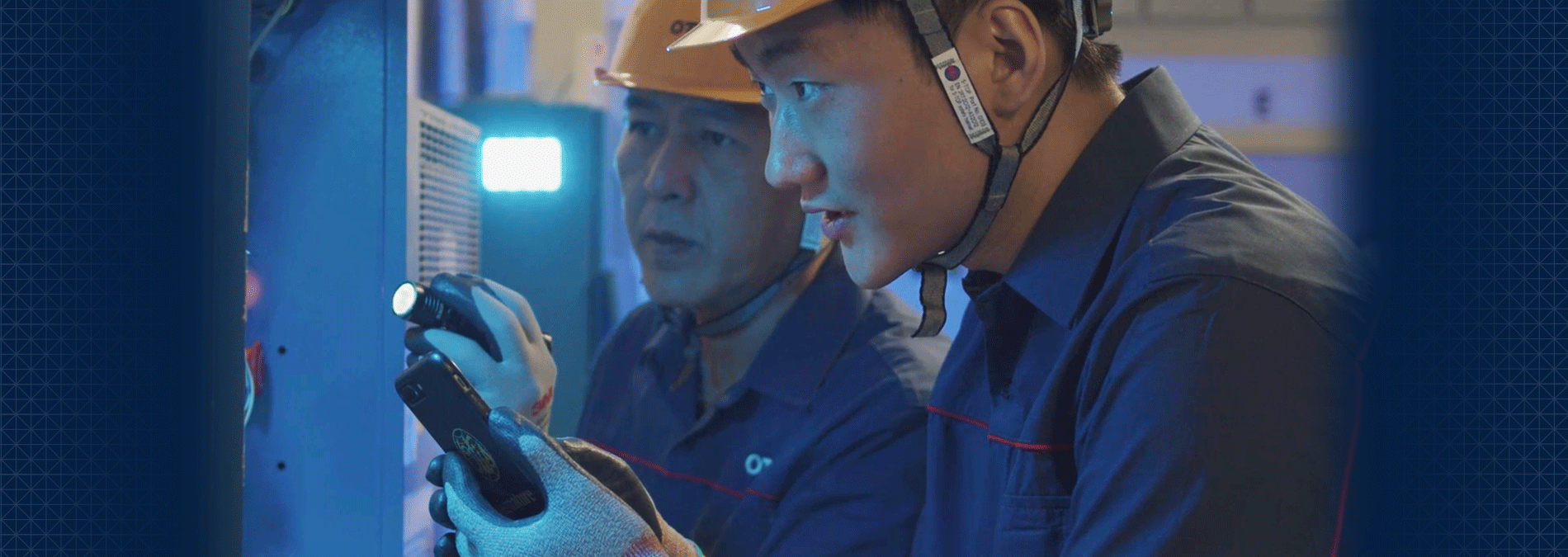
Our colleagues keep people moving
Hear what our mechanics are saying
Going Digital at Otis: How Otis ONE™ helps both mechanic and customer
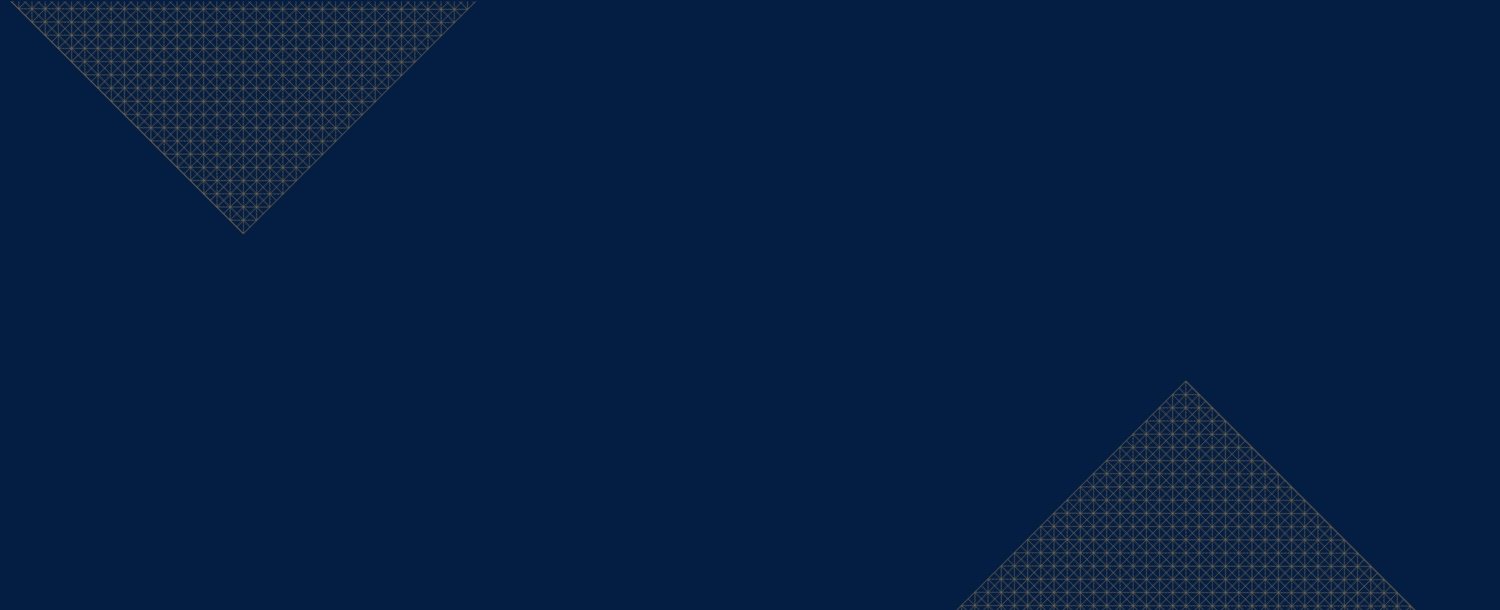
Hear what our mechanics are saying
In China, Otis ONE™ is revolutionizing the way we deliver Service
After working for nearly a decade as an Otis field professional in China, Sailong W. knows what to expect on the job. This includes staying on a tight schedule, anticipating requests from his customers and property managers, preparing for government inspections, and keeping the elevators under his watch running efficiently and safely for his passengers.
Efficiency is important for Sailong as more people in China continue to move into cities. Today, more than 60% of China’s population live in cities, and that number is projected to approach close to 1.1 billion people by 2050*.
In 2018, Otis China launched Otis ONE, a new digital service platform powered by the Internet of Things (IoT). Sailong says this platform has significantly improved the service he provides to his customers.
What impressed me most was the first time I received a fault notification,
Sailong explains. At the time, an elevator car door was stuck open by an object and could not close.
Sailong stopped what he was doing and drove to the job site. When he arrived, he confirmed the issue was exactly what his Otis ONE fault alert flagged and solved the problem quickly. When the property management arrived, the elevator had already resumed operations before any resident even noticed.
For an elevator technician who had spent years visiting job sites after receiving a call from a customer, fixing the problem before his customer even knew about it was revolutionary.
I deep dived into studying the features of Otis ONE, asking my colleagues to join me and learn together,
Sailong says. All the data for the elevators are on display on our mobile devices. The information supports us in making educated judgments in carrying out service work.
Unsurprisingly, Sailong's customers are benefiting from Otis ONE as well with increased uptime and fewer service disruptions.
Learn more about Otis ONE and how it is bringing the next generation of service to our customers.
*According to data from Statista
Modern technology helps to provide a personalized touch
All of his customers know Otis mechanic Damon P. on a first-name basis. He wouldn’t have it any other way.
They have my phone number, and I talk with each one frequently,
Damon says. There doesn’t have to be a service-related reason to have a conversation. I just really like the people I work with.
Having strong customer relationships helps Damon feel connected to his customers, so he can more quickly assess their needs. Couple that with the power of Otis ONE IoT technology that connects elevators to the cloud and provides cutting-edge insights your equipment. This puts Damon ahead of the curve when he is needed most.
A customer called me to say two of their elevators were down,
Damon explains. I pulled up the Otis ONE app and saw that one car would be easier to fix because of the type of repair. So when I arrived, I focused on getting that unit running first because I knew that would minimize downtime.
Otis ONE was designed to meet the evolving needs of our customers by connecting elevators to the cloud. Putting modern, digital technologies in the hands of our expert technicians provides an unmatched level of customer service that also helps demystify what elevators are capable of in today’s world.
Elevators are becoming more digital every day, and I take pride in talking about the value of adding Otis ONE to my customers’ buildings.
An Otis mechanic identified an elevator shutdown with Otis ONE™—before the customer even noticed
Located near one of the world’s busiest airports is a multi-story office complex boasting over 580,000 square feet of office and conference space. Thousands of office workers and conference guests rely on the building’s numerous elevators to get where they need to go each day. One early Monday morning last year, an elevator in the building was out of service in need of repair. To get it up and running, onsite technician support was needed. And on this particular day, the property was hosting a major conference, which made the situation even more critical. The shutdown had the potential to cause massive delays.
Luckily, Bernd J., an Otis mechanic with more than 30-years of experience, saw the problem on his Otis ONE app early that morning as soon as he started his day. The Otis ONE IoT digital platform uses artificial intelligence, machine learning and cloud technology to provide our mechanics with predictive maintenance insights and our customers with real-time information on the status of their elevators.
I usually check the app during breakfast to see if everything is ‘green’ — which means all units are running smoothly,
Bernd says. On this day, Bernd noticed one of the elevators at the customer site was shutdown requiring onsite support. Bernd hopped into his Otis van and was onsite by 7:30 a.m. The customer was surprised – and also very pleased – to see him there as the building staff had not yet noticed there was an elevator requiring repair.
Bernd’s dedication, supported by Otis ONE technology, allowed him to get the elevator back up and running before most of the office staff and conference guests had even arrived. The bottom line is Otis ONE means faster troubleshooting and higher system reliability for our customers,
added Bernd.
How Otis ONE™ keeps one university campus moving forward
Nestled in the heart of Atlanta, Georgia, an Otis customer brings together thousands of students and administrative staff members each semester to create the next generation of world leaders. With that mission in mind, keeping everyone moving on campus is essential.
The university relies on over 200 elevators, each one playing a key role in keeping students, faculty and administrators on the move. When an elevator is down, it disrupts operations and risks taking time away from the students' education.
Otis field professional Dwight P., responsible for elevator maintenance on campus, appreciates this. So he uses a different kind of learning — machine learning — with his Otis ONE™ app to save time on the job and keep his team working efficiently. The Otis ONE digital IoT platform uses artificial intelligence, machine learning and cloud technology to provide our customers with real-time information and our mechanics with predictive maintenance insights that help enhance elevator uptime.
On every call, I used to have to go to the machine room and sign into the controller to look at the fault log before I could even get started,
said Dwight. But with Otis ONE, it's all right in front of me on my smart phone, and it saves me valuable time on the job.
Otis ONE also helps Dwight prioritize which elevators need attention first, especially when multiple units across campus are reported to need service at once. Sometimes when an elevator is reported as not functioning, it's a false report, according to Dwight, so the Otis ONE solution helps the team on the ground assess the situation quickly.
Users sometimes report an elevator as not functioning by mistake or simply walking away while waiting, not realizing the elevator is running a diagnostic check,
said Dwight. With Otis ONE, I can see how recently an elevator door cycled — meaning how frequently it opened and closed — which allows me to see if a unit is actually out of service or not. This information helps me prioritize calls more effectively and keeps my team from ping-ponging all over campus, saving lots of time.
Learn more about Otis ONE and how it can save your site time and money.